Precision Mold Manufacturer: Elevating Quality in Metal Fabrication
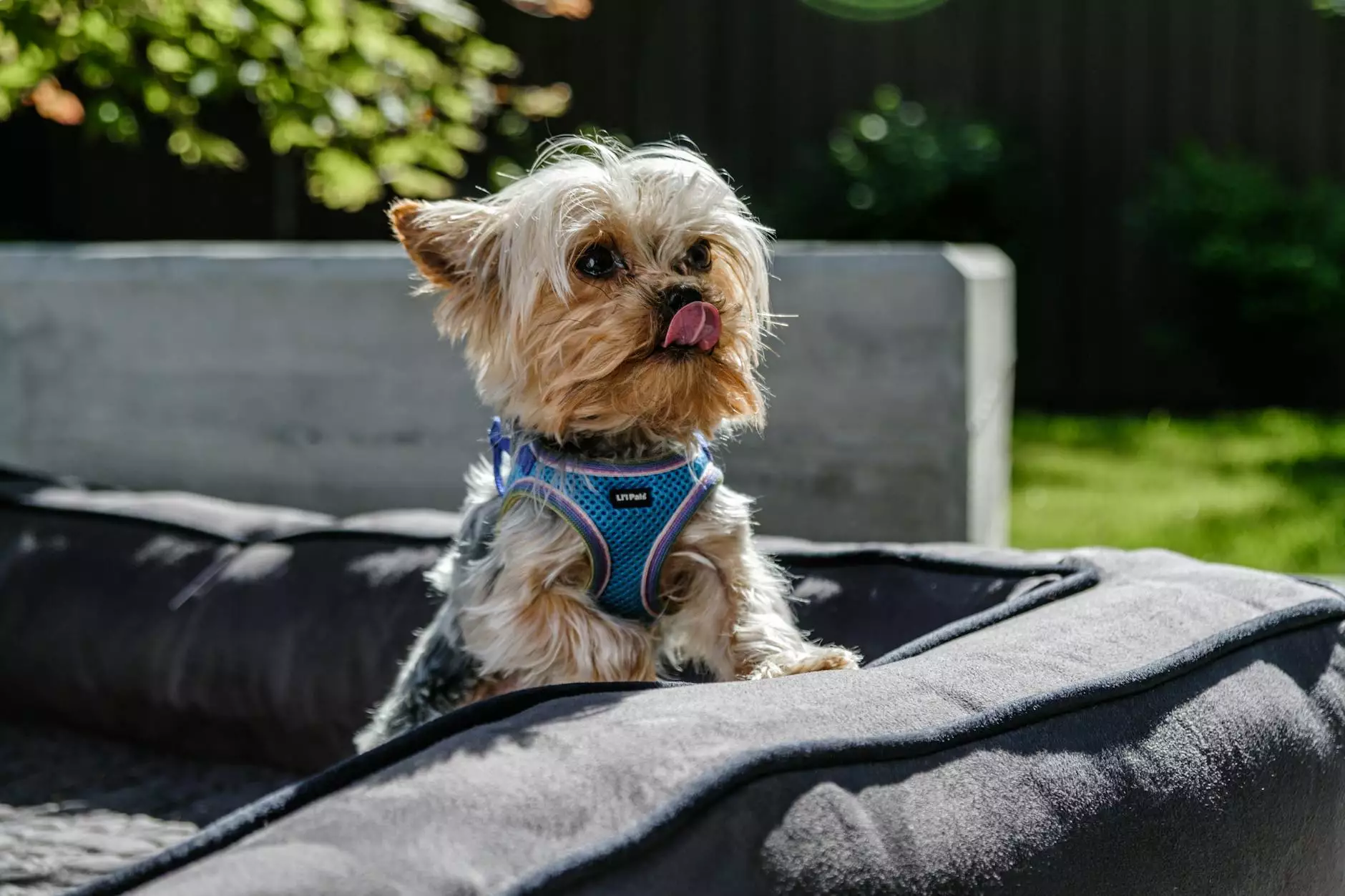
In the competitive landscape of manufacturing, being a proficient precision mold manufacturer can set a business apart. The process of mold creation is not merely about crafting forms; it's about driving innovation, enhancing production efficiency, and ensuring product quality in every piece. In this comprehensive article, we will delve into the intricacies of the business, exploring the significance of precision molds, the methodologies employed by top manufacturers, and how these elements coalesce to benefit sectors like automotive, aerospace, consumer goods, and more.
The Importance of Precision in Mold Manufacturing
Precision in mold manufacturing is paramount. It ensures that each product produced is consistent and meets the required specifications. While many manufacturers may overlook this vital aspect, a precision mold manufacturer recognizes that:
- Product Quality: Every mold must be crafted to exact specifications to ensure that the finished product is free from defects.
- Cost Efficiency: High precision reduces the need for reworks and wastage, ultimately cutting costs.
- Reputation and Reliability: Companies known for their precision gain the trust of clients, which leads to repeat business and referrals.
Understanding the Mold Manufacturing Process
The process of creating a mold involves several critical stages, each requiring meticulous attention to detail. As a precision mold manufacturer, we employ advanced techniques to ensure quality at each step:
1. Design and Prototyping
The journey begins with a robust design phase. Utilizing CAD (Computer-Aided Design) software, designers create detailed 3D models of the mold. This stage often includes:
- Feasibility Analysis: Assessing whether the design can be correctly and efficiently manufactured.
- Material Selection: Choosing the right materials that will withstand the pressures of production.
2. Tooling and Fabrication
Once the design is finalized, tooling begins. This stage involves:
- Machining Processes: Advanced CNC machines are used to carve out the details of the mold, ensuring accuracy.
- Surface Finishing: Treatments are applied to achieve the desired texture and smoothness, vital for optimal product performance.
3. Testing and Quality Assurance
A precision mold manufacturer must never compromise on quality assurance. This step includes:
- Mold Trials: Initial test runs are conducted to determine if the mold produces parts that meet specifications.
- Adjustments and Final Inspections: Any necessary adjustments are made before the mold is finalized for production use.
The Role of Technology in Precision Mold Manufacturing
Today's precision mold manufacturers harness the potential of advanced technologies. The integration of Industry 4.0 allows for:
- Automation: Streamlining the manufacturing process, reducing human error, and increasing output.
- Data Analytics: Using data to inform decisions on design and production, leading to continual improvement.
- 3D Printing: Rapid prototyping of molds before full-scale production, saving time and resources.
Industries Benefiting from Precision Mold Manufacturing
Precision molds play an integral role across various industries. Here are a few key sectors that rely heavily on sophisticated mold production:
1. Automotive Industry
The automotive sector uses precision molds for:
- Parts Production: Components like dashboards, bumpers, and casings.
- Improved Safety Standards: High-quality molds ensure that car parts meet strict safety regulations.
2. Aerospace Sector
In aerospace, precision is non-negotiable. Molds are used for:
- Engine Components: Critical in performance and safety.
- Interior Structures: Lightweight designs that maintain strength.
3. Consumer Goods
From electronic casings to household items, precision molds ensure that:
- Consistency: Each unit produced matches the intended design.
- Functionality: Products perform as expected, enhancing customer satisfaction.
Choosing the Right Precision Mold Manufacturer
When selecting a precision mold manufacturer, consider the following factors to ensure reliability and quality:
- Experience and Expertise: Look for manufacturers with a proven track record.
- Technological Capabilities: Ensure they utilize modern machinery and techniques.
- Quality Certifications: ISO certifications or industry-specific standards indicate commitment to quality.
- Customer Service: Responsive and supportive manufacturers will make collaboration easier.
Conclusion: The Future of Precision Mold Manufacturing
The role of a precision mold manufacturer is becoming increasingly significant as industries demand higher quality and efficiency. With continual advancements in technology and manufacturing processes, businesses like DeepMould.net are poised to lead the way towards a future dominated by high precision, reduced waste, and unparalleled product quality.
Choosing a reliable precision mold manufacturer is not just a business decision; it’s a step towards ensuring that your products meet the high standards required in today's competitive market. By focusing on precision, quality, and innovation, manufacturers are not just meeting the demands of the current market but are also setting the stage for future growth and success.