Exploring Tube Connection Types: A Comprehensive Guide
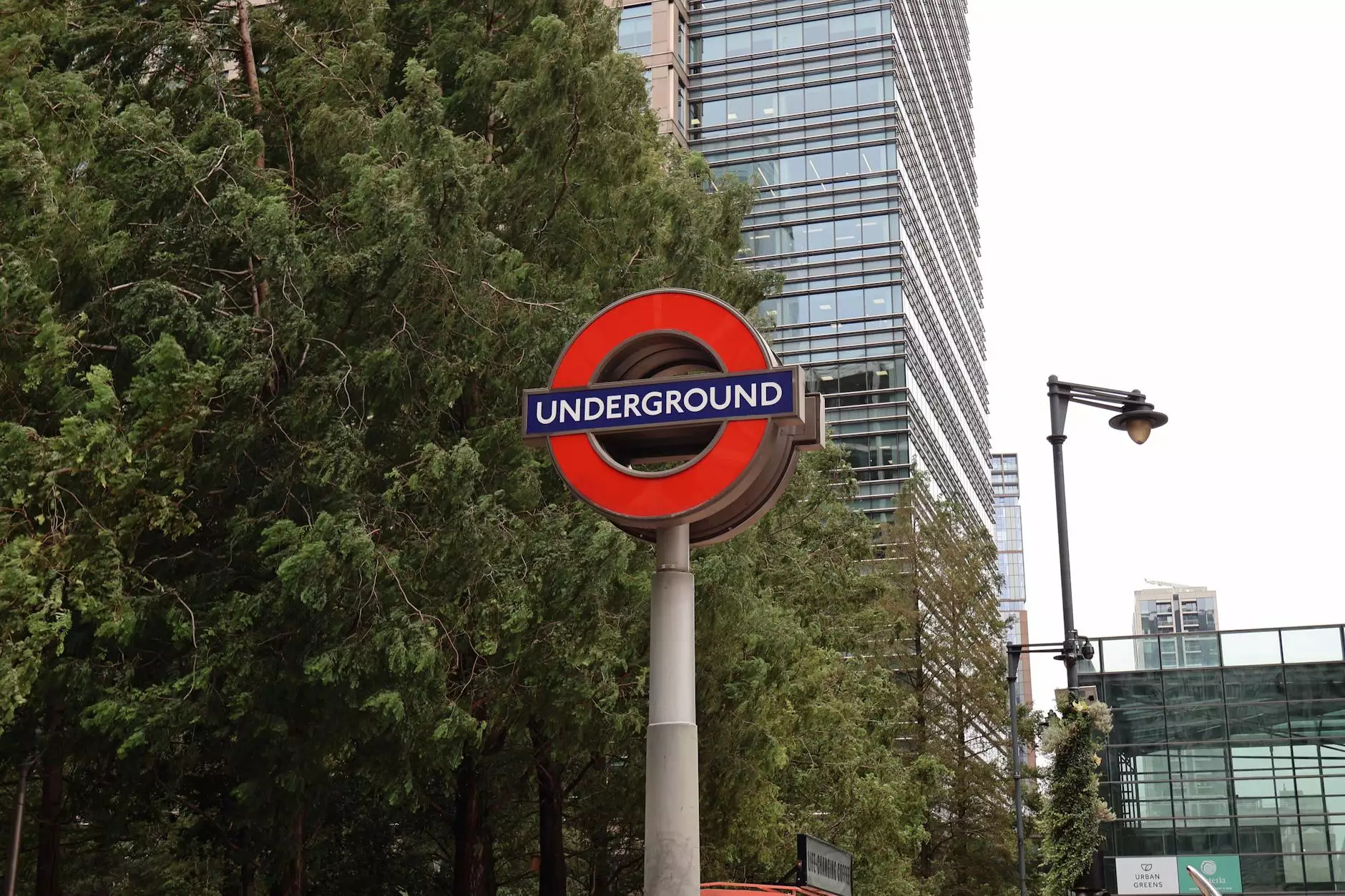
When it comes to industrial applications, selecting the right tube connection types is crucial for ensuring efficiency, safety, and optimal performance. Different projects require unique solutions, and understanding the variety of available fittings and their specific purposes is essential. In this extensive guide, we will delve into various tube connection types, including tube fittings, ferrule fittings, forged pipe fittings, and more.
1. Understanding Tube Connection Types
Tube connection types refer to the various methods and fittings used to join tubes in fluid systems, ensuring a tight, leak-resistant seal. The choice of tube connections can greatly impact the performance of a system, and therefore, it is critical to understand the characteristics and applications of each type.
1.1 Importance of Selecting the Right Connection Type
Choosing the appropriate tube connection type is essential for several reasons:
- Safety: Proper connections reduce the risk of leaks, which can lead to hazardous situations in industrial environments.
- Efficiency: Well-designed connections ensure maximum flow rates and minimal pressure drop, optimizing system performance.
- Cost-Effectiveness: Selecting the right type can reduce maintenance costs and prolong the lifespan of components.
- Compatibility: Different fluids and gases require specific materials and designs to avoid corrosion and degradation.
2. Types of Tube Connections
Let's explore the most common tube connection types used in industry today.
2.1 Tube Fittings
Tube fittings are essential components that connect two tube sections and can be classified into several subcategories:
2.1.1 Compression Fittings
Compression fittings are widely used for a variety of applications. They work by compressing a sleeve onto the tube's surface, creating a tight seal. Common materials for compression fittings include brass, stainless steel, and plastic. Here are some advantages:
- Easy Installation: They require no special tools for assembly.
- Versatility: Suitable for both rigid and flexible tubes.
- Reusability: Can be disassembled and reassembled, making them ideal for maintenance.
2.1.2 Flare Fittings
Flare fittings provide a robust connection by deforming the tube end to create a flared surface. They are especially beneficial in high-pressure systems:
- High Pressure Capabilities: Ideal for high-pressure applications.
- Leak Resistance: The flared connection forms a tight seal without the need for additional seals.
2.2 Ferrule Fittings
Ferrule fittings utilize a ferrule (a small cylindrical piece) to secure the tube in place. There are two main types of ferrule fittings:
2.2.1 Single Ferrule Fittings
These fittings utilize one ferrule to create a seal between the tube and the fitting. They are simple and effective for a wide range of applications.
2.2.2 Double Ferrule Fittings
Double ferrule fittings offer increased reliability, especially in high-vibration environments or when used with high-pressure lines. They offer enhanced grip and seal:
- Reduced Vibration: Designed to withstand vibrations and movement.
- Leak-Proof: Provide a more secure connection due to the double ferrule design.
2.3 Forged Pipe Fittings
Forged pipe fittings are created through a forging process, which strengthens the fittings by aligning the grain structure. They are commonly used in high-pressure applications:
- Durability: Highly resistant to wear and tear.
- High Strength: Capable of withstanding extreme pressures.
2.4 Threaded Pipe Fittings
Threaded pipe fittings are among the most straightforward connection types. They feature external and internal threads that allow for easy assembly and disassembly:
- Ease of Use: Simple to install and require minimal tools.
- Variety of Materials: Available in brass, steel, and PVC, suited for various applications.
3. Selecting the Right Tube Connection
When it comes to choosing the best tube connection types, several factors must be taken into account:
3.1 Application Requirements
Identify the application's specific requirements, such as pressure, temperature, and media type. This will guide you toward the most suitable connection type.
3.2 Material Compatibility
The selected materials for fittings should be compatible with the tube's material to avoid leaching or corrosion. Common materials include:
- Stainless Steel: Offers excellent corrosion resistance, ideal for harsh environments.
- Brass: Good for water and gas applications but less resistant to corrosion.
- Plastic: Lightweight and resistant to chemical corrosion, suitable for less demanding applications.
3.3 Pressure and Temperature Considerations
The pressure and temperature limits of the connection type must match the operational conditions of your system to ensure longevity and prevent failures.
4. Advantages of Using Quality Tube Connection Types
Investing in high-quality tube connection types can offer several advantages:
4.1 Enhanced Performance
Quality connections ensure optimal flow rates and pressure retention, which is crucial for efficient system operation.
4.2 Reduced Leaks
Superior design and materials help in minimizing leaks, which can lead to significant costs and safety hazards.
4.3 Long-term Cost Savings
While initial investments may be higher, the durability and reliability of quality fittings often result in lower overall maintenance and replacement costs.
5. Conclusion
In conclusion, understanding the various tube connection types is crucial for anyone involved in designing, installing, or maintaining industrial systems. From tube fittings to forged pipe fittings and beyond, each type of connection has unique benefits and applications. By selecting the most suitable connection for your needs, you can ensure safety, performance, and reliability in your operations.
For any business focused on providing quality fittings and connections, such as techtubes.in, it is essential to stay informed about the latest technologies and standards in tube connections. As industries evolve, so do the requirements for connections, pushing towards more innovative and efficient solutions.