CNC Lathe Machine Parts and Components: An In-Depth Guide
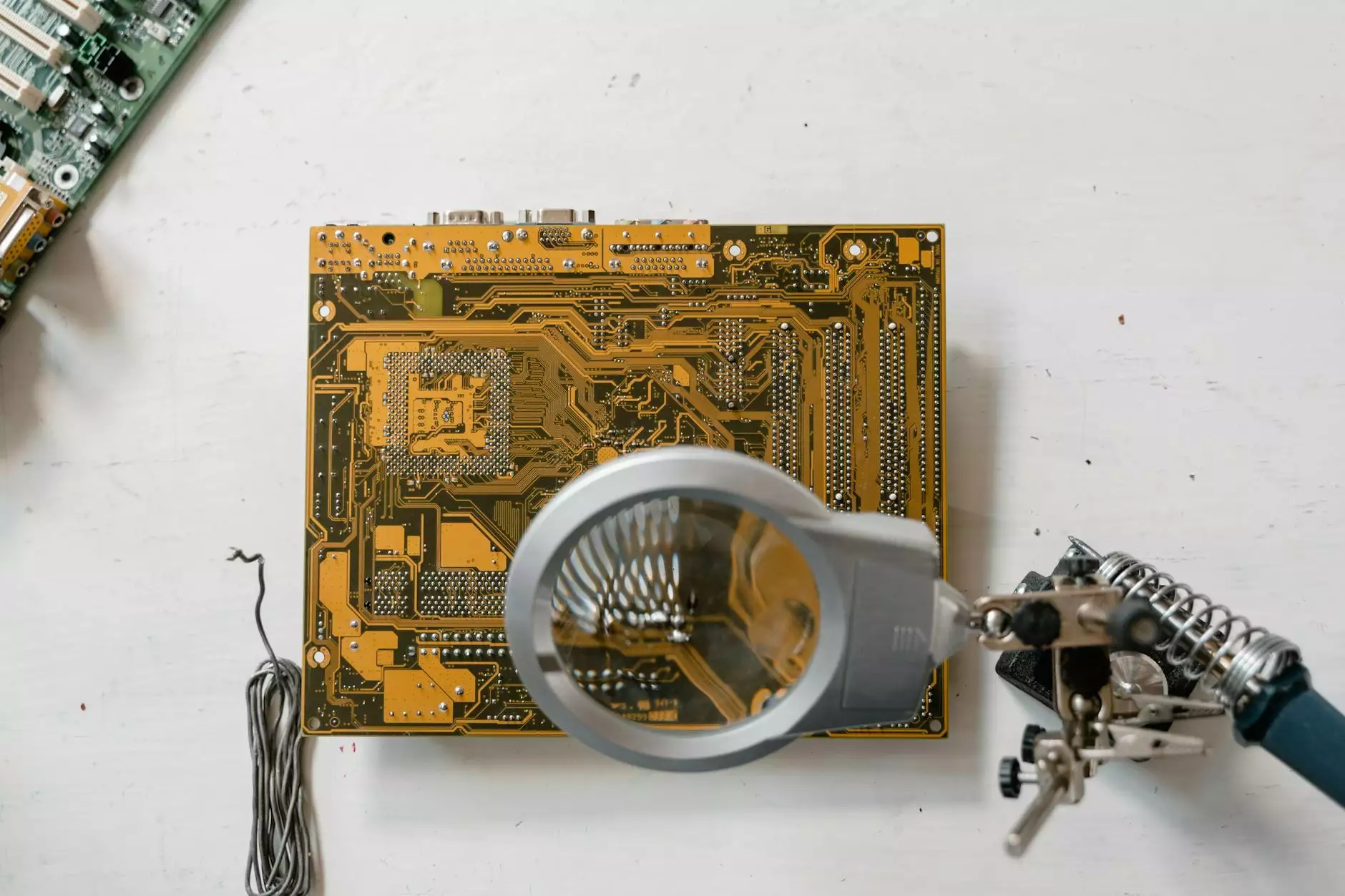
The world of CNC lathe machine parts and components plays a crucial role in the efficiency and precision of modern manufacturing. These machines revolutionize the metal fabrication industry, offering remarkable capabilities in shaping and designing complex parts. In this article, we will delve deep into the various components that make up CNC lathes, their functionalities, and their significance in production processes.
Understanding CNC Machining
CNC, or Computer Numerical Control, machining is a method where pre-programmed computer software controls the movement of factory tools and machinery. This technology enables manufacturers to produce parts with high accuracy and repeatability. CNC lathes specifically are designed to swing material against a cutting tool, allowing for the creation of cylindrical parts.
The Importance of CNC Lathe Machines
CNC lathes are integral to the metal fabrication industry for several reasons:
- Precision: CNC machines offer high levels of precision that manual machines cannot replicate.
- Efficiency: They can operate continuously, leading to increased production rates and reduced human error.
- Complex Designs: CNC lathes can create complex geometries that are difficult to achieve through manual processes.
- Material Versatility: These machines can work with a variety of materials, including metals, plastics, and composites.
Key CNC Lathe Machine Parts and Components
The functionality of CNC lathes relies on several critical parts that work in unison to deliver high performance. Below is a detailed overview of each component:
1. Headstock
The headstock is one of the primary components of a CNC lathe. It houses the spindle and the motor that drives the spindle. Key functions of the headstock include:
- Supporting the rotating spindle.
- Controlling the speed and direction of the spindle rotation.
- Facilitating the attachment of various tools through tool holders.
2. Tailstock
The tailstock is positioned opposite the headstock and is used to support long workpieces. Its components have additional features such as:
- Providing stability during machining operations.
- Housing tools for drilling operations.
- Adjusting the height and position of the workpiece.
3. Bed
The bed of the CNC lathe is the structure that supports the headstock and tailstock. Its construction is critical for maintaining alignment and stability during machining. Key considerations for the bed include:
- Material strength to withstand vibrations and operational forces.
- Surface finishes for accurate movement of components.
- Design to allow easy access for maintenance and cleaning.
4. Cross Slide
The cross slide enables lateral movement of the tool holder, allowing for precise cutting in a horizontal plane. Its importance includes:
- Facilitating intricate machining operations.
- Providing adjustments for depth of cut.
- Enabling the operator to quickly reposition the tool.
5. Tool Turret
The CNC tool turret holds multiple cutting tools, allowing for quick changes without manual intervention. This component is essential for:
- Minimizing downtime during machining processes.
- Improving productivity by allowing various operations to be performed on a single setup.
- Optimizing tool usage with various cutting applications.
6. Spindle
The spindle is the rotating axis of the CNC lathe that holds the workpiece. Its features include:
- High-speed rotation capabilities for increased cutting efficiency.
- A variety of attachment methods for different workpiece sizes.
- Precision bearings to minimize run-out and enhance accuracy.
7. CNC Control System
The CNC control system is the brain of the lathe machine, interpreting G-code commands to control machine functions. Key aspects of CNC control systems include:
- User interface for easier programming and operation.
- Ability to store multiple programs for different machining tasks.
- Integration with CAD/CAM software for seamless design-to-production workflows.
8. Linear Guides and Ball Screws
Linear guides and ball screws enable precise movement of the CNC lathe's components. Their characteristics include:
- Reduced friction for smoother motion.
- High efficiency in translating rotational motion into linear motion.
- Enhanced durability with proper lubrication and maintenance.
Types of CNC Lathe Machining Operations
CNC lathes are versatile and can perform various operations tailored to fit specific manufacturing needs. The common types of operations include:
- Turning: Removing material from the workpiece to create cylindrical shapes.
- Facing: Trimming the ends of a workpiece to achieve a flat surface.
- Boring: Enlarging pre-existing holes with precision.
- Threading: Cutting threads into the surface of a workpiece.
- Grooving: Creating grooves or channels for further applications.
Applications of CNC Lathe Machines
The applications of CNC lathe machines parts and components are extensive across many industries. Some of the most prominent applications include:
- Aerospace: Manufacturing parts for aircraft and spacecraft with strict tolerances.
- Automotive: Producing components like shafts, gears, and housings for vehicles.
- Medical Devices: Creating precise instruments and surgical components.
- Electronics: Manufacturing enclosures and connectors for electronic devices.
- General Engineering: Providing customized solutions for various engineering projects.
Choosing the Right CNC Lathe for Your Business
When selecting a CNC lathe, consider factors such as:
- Size and Capacity: Determine the maximum size of workpieces you plan to manufacture.
- Power and Speed: Choose a machine that offers the right balance of power and speed for your specific applications.
- Control System: Opt for a user-friendly CNC control system that easily integrates with existing software.
- Investment and ROI: Analyze the total cost of ownership and potential return on investment.
Maintenance of CNC Lathe Machines
Regular maintenance is essential to ensure the longevity and efficiency of CNC lathe machines. Important maintenance practices include:
- Regular Cleaning: Keep the machine free from debris and coolant to avoid damage.
- Lubrication: Lubricate moving parts to reduce wear and improve performance.
- Calibration: Regularly calibrate the machine to maintain precision and accuracy.
- Software Updates: Keep the CNC software updated to benefit from new features and enhancements.
Conclusion
The world of CNC lathe machine parts and components is instrumental in modern manufacturing, particularly within the metal fabrication industry. Understanding the various components and their functions can greatly enhance your production capabilities. As you navigate through the complexities of CNC machining, remember that investing in quality machinery, coupled with proper maintenance, can lead you to achieve outstanding results in your engineering and manufacturing endeavors.
For more insights into CNC machining and to explore our range of services at DeepMould.net, visit our website. Join us in advancing precision engineering with cutting-edge technology and expertise.